Construction of walls with foam concrete
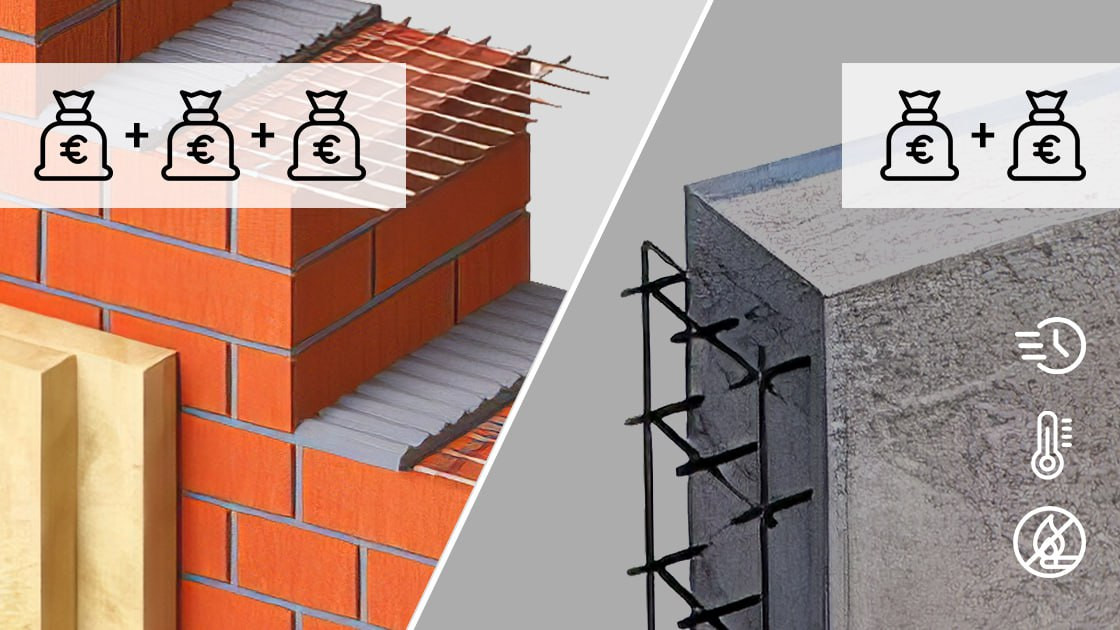
When choosing a material for building walls, we suggest considering monolithic foam concrete as a material. Attention! Not a foam concrete block, but a monolithic filling with foam concrete. To understand the advantages, I propose to compare it with the popular Serbian technology of erecting brick walls, followed by insulation and finishing.
Brick loses to monolithic foam concrete
The brick itself is reliable and proven material, but if you take into the costs of all stages of work, then the final price per m2 of wall may upset you. From the estimate, it will not be possible to exclude the inevitable work associated with providing power supply (technical grooves for sockets, switches, etc.), plastering, priming and puttying. If the walls are external and should protect the house from cold and heat, the cost of insulation and finishing work, the insulation itself and the material of the crate will have to be added to the estimate. The average service life of the insulation is 30-50 years, resistance to leaks and fire is extremely doubtful.
Advantages and benefits of building walls with monolithic foam concrete
The construction of foam concrete walls eliminates many costs. Foam concrete is poured into the formwork where cable channels, landing clips for mounting sockets and switches, shafts for water or sewer pipes are obviously laid.
The thermal conductivity (thermal insulation properties) of monolithic foam concrete is the same as that of wood. Established by building codes thermal protection index Rq min = 2.8 m2 x K / W is achieved without the use of heaters with a wall thickness of 50 cm.
The processing of a wall made of monolithic foam concrete is minimized. The wall after dismantling the formwork is almost perfectly flat, although it will require processing with a special primer, followed by puttying and painting.
The process of erecting walls with foam concrete
Specialists deliver the necessary equipment, formwork and materials to the facility under construction.
According to the plan and technical documentation, the formwork is mounted.
They start reinforcing elements, cable channels, landing clips for mounting sockets and switches, mines for water or sewer pipes.
The walls are poured with foam concrete in layers - 0.6 meters each, after which the formwork panels are moved to a higher level and the procedure is repeated until the wall is completely ready. Thus, a minimum set is sufficient plastic-formwork, which also reduces costs.
After removing the formwork panels, it is required to prepare the surface for painting or finishing with decorative material.
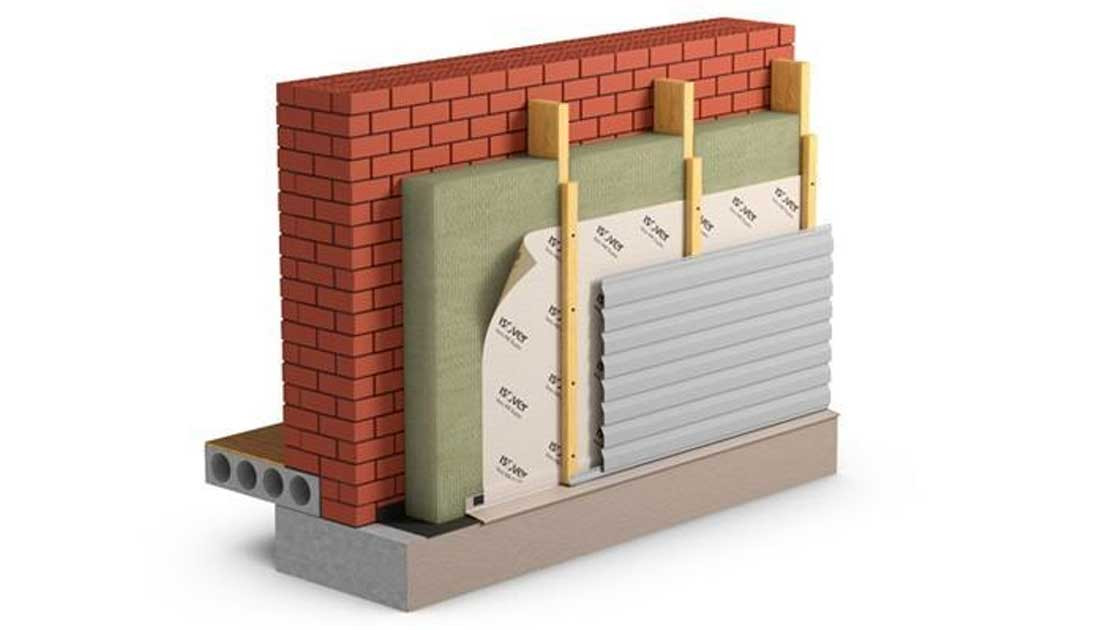
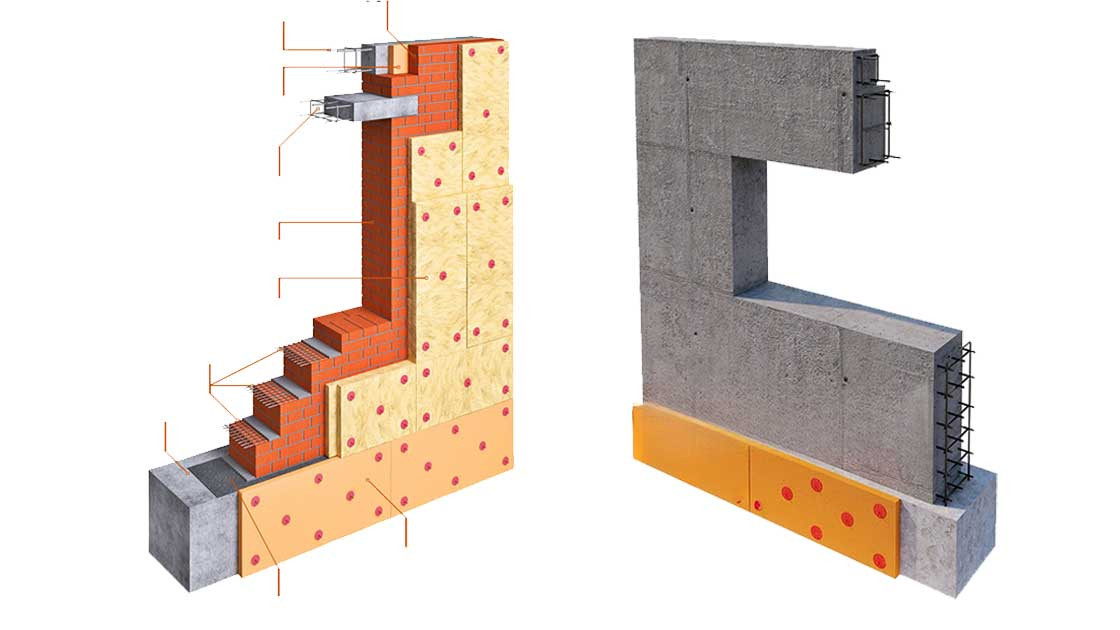
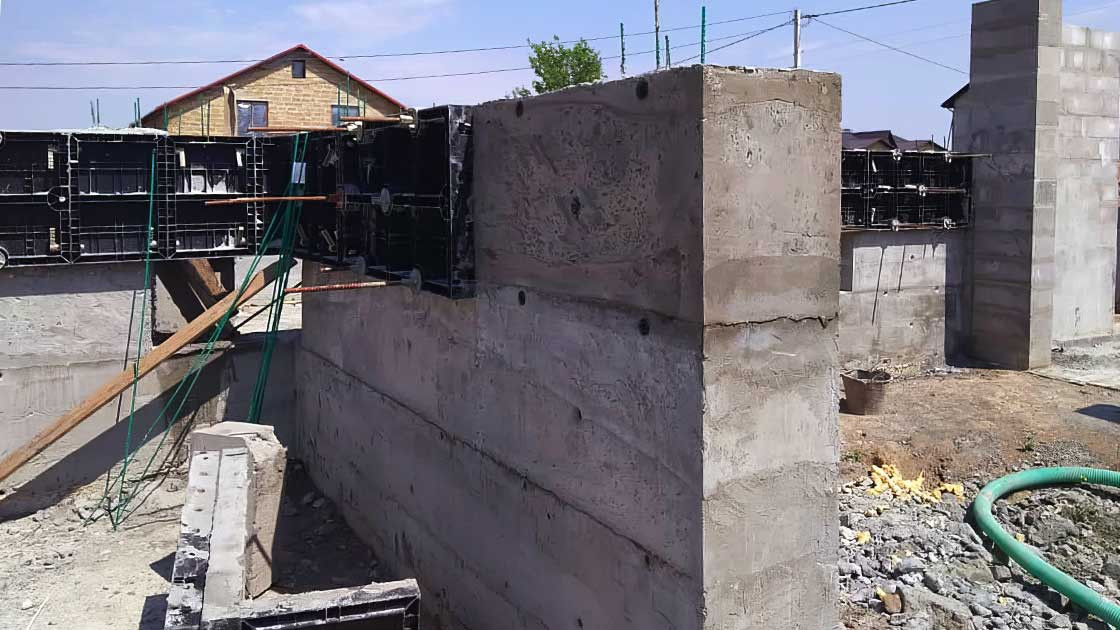